Dans cet article
La réduction de la consommation d'énergie dans l'industrie
Les moteurs électriques sont courants dans l'industrie et représentent une grande partie de la consommation d'énergie d'une organisation. L'Union européenne compte aujourd'hui huit milliards de moteurs électriques en service consommant près de 50 % de l'électricité produite dans l'Union.
Mais saviez-vous que réduire la consommation d'énergie électrique de votre moteur est le moyen le plus efficace d'économiser et d'améliorer le coût total de possession (TCO) de votre moteur ? En effet, 97 % du TCO est entièrement dû au coût de l'énergie électrique. Le prix d'achat d'un nouveau moteur ne représente que 1 % du TCO et la maintenance ajoute 2 % supplémentaires.
Un contrôle régulier des performances de votre moteur vous permet un fonctionnement aussi efficace que possible en termes d'énergie et de coûts. Il faut cependant tenir compte de nombreux éléments lors de l'évaluation d'un moteur, par exemple les exigences légales, les coûts totaux de fonctionnement et la taille du moteur.
Choisir un moteur qui est tout simplement conforme à la réglementation pourrait en fait coûter des milliers d'euros à votre entreprise. En tenant compte du TCO, vous maintenez un maximum d'efficacité, tout en protégeant les résultats de l'entreprise.
Comprendre les réglementations sur l'efficacité des moteurs
L'efficacité énergétique des moteurs a beaucoup progressé depuis les années 1960. Les moteurs sont passés d'un rendement de 88 % en 1960 à 95,8 % en 2013 (comme le montre la figure 1)
Les gouvernements et les agences reconnaissant les effets positifs des moteurs électriques écoénergétiques sur la réduction de la consommation et des émissions, des normes d'efficacité sont désormais appliquées dans le monde entier.
Par exemple, en 1999, le Comité européen des constructeurs de machines électriques (CEMAP/UE) a introduit un système volontaire pour une gamme limitée de moteurs. Celle-ci a depuis évolué et en 2009, la Commission électrotechnique internationale (CEI) a créé une nouvelle norme. La norme CEI 60034-30 définit les classes internationales d'efficacité énergétique et établit les méthodes d'essai pour déterminer les pertes d'énergie.
Les classes d'efficacité énergétique sont définies comme suit :
- IE1 - Rendement standard
- IE2 – Rendement élevé
- IE3 – Rendement premium
- IE4 – Rendement super-premium
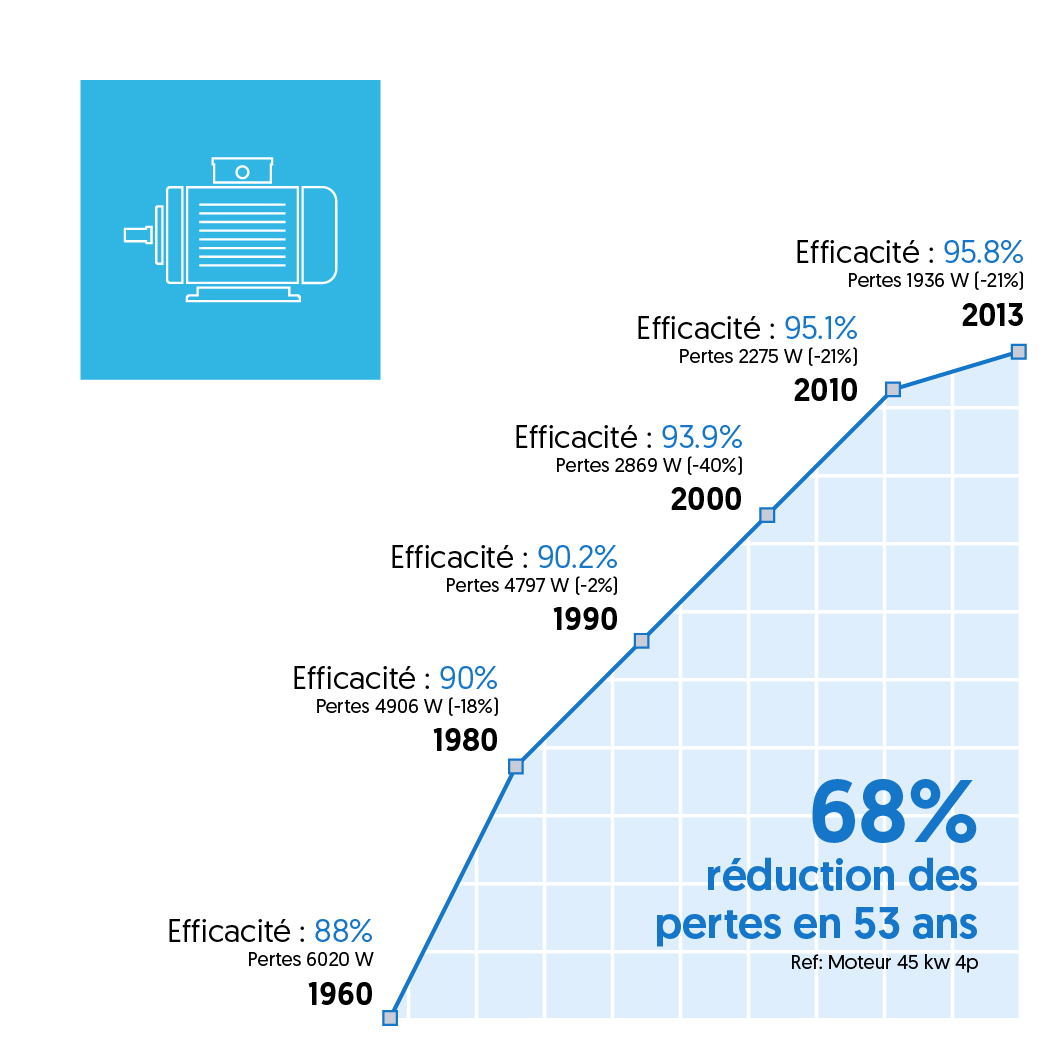
Figure 1 – Comment l’efficacité des moteurs a évolué au fil des ans.
L'efficacité de chaque classe est définie pour une plage de puissance nominale de 0,75 à 375 kW et est calculée comme le rapport entre la puissance de sortie mécanique et la puissance d'entrée électrique. Un moteur électrique IE3 peut atteindre un rendement d'environ 96 % (selon la puissance et la vitesse) et un moteur IE4, un rendement d'environ 97 %.
Un classement IE5 encore plus efficace, appelé « ultra-premium », sera prévu pour les futures mises à jour réglementaires. La perte d'énergie avec un moteur IE5 sera environ 20 % inférieure à la perte avec un moteur IE4.
La perte d'énergie avec un moteur IE5 sera environ 20 % inférieure à la perte avec un moteur IE4. Notre principal fournisseur, WEG, peut produire des moteurs IE5 avec la technologie asynchrone standard pour des puissances de moteur à partir de 75 kW.
Ces normes ont été appliquées conformément à la directive européenne sur l'écoconception 2009/125/CE, qui a été établie pour spécifier les exigences relatives à la conception écologiquement responsable des produits liés à l'énergie (ErP).
Respecter la législation la plus récente
Le dernier règlement sur l’écoconception, introduit en octobre 2019 est le règlement UE 2019/1781. Il décrit deux phases pour faire progresser les niveaux d'efficacité énergétique et s'applique aux moteurs électriques à induction basse tension dont la tension nominale est inférieure à 1 000 V en courant alternatif (CA) et aux variateurs de vitesse (VSD), également appelés convertisseurs de fréquence. Voir la figure 2 pour une vue d'ensemble des normes IE.
Rendre IE3 obligatoire en Phase 1
En juillet 2021 :
- Il est devenu obligatoire pour tous les moteurs 0,75 kW – 1000 kW, 2-4-6-8 pôles, de respecter la norme de rendement premium IE3. Il n'est plus possible de combiner un moteur IE2 avec un VSD pour atteindre les niveaux de rendement IE3.
- La réglementation s'applique aux moteurs monovitesse triphasés 50 Hz, 60 Hz, 50/60 Hz pour un fonctionnement direct en ligne en service continu défini comme S3 ≥ 80 % et S6 ≥ 80 %.
- La réglementation s'applique également aux moteurs qui étaient auparavant exemptés, par exemple, les moteurs ATEX avec les types de protection EX ec, EX d, Ex de, Ext, les moteurs avec refroidissement IC418, et les moteurs à frein externe.
- FLes niveaux d'efficacité IE2 sont obligatoires pour les moteurs triphasés dont la puissance nominale est comprise entre 0,12 kW et 0,75 kW.
- Il est également obligatoire pour tous les VSD entre 0,12 et 1.000 kW d'avoir une perte de puissance correspondant à un minimum de IE2.
Il y a quelques exceptions à cette règle, comme le montre la figure 3.
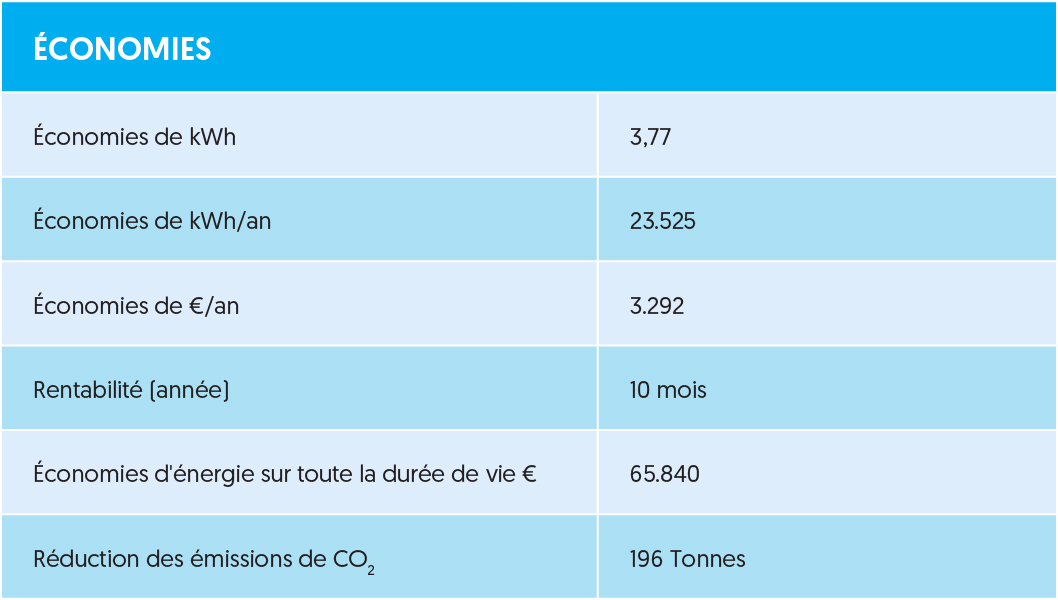
Figure 2 – économies calculées en remplaçant un vieux moteur par un moteur plus efficace de classe IE3
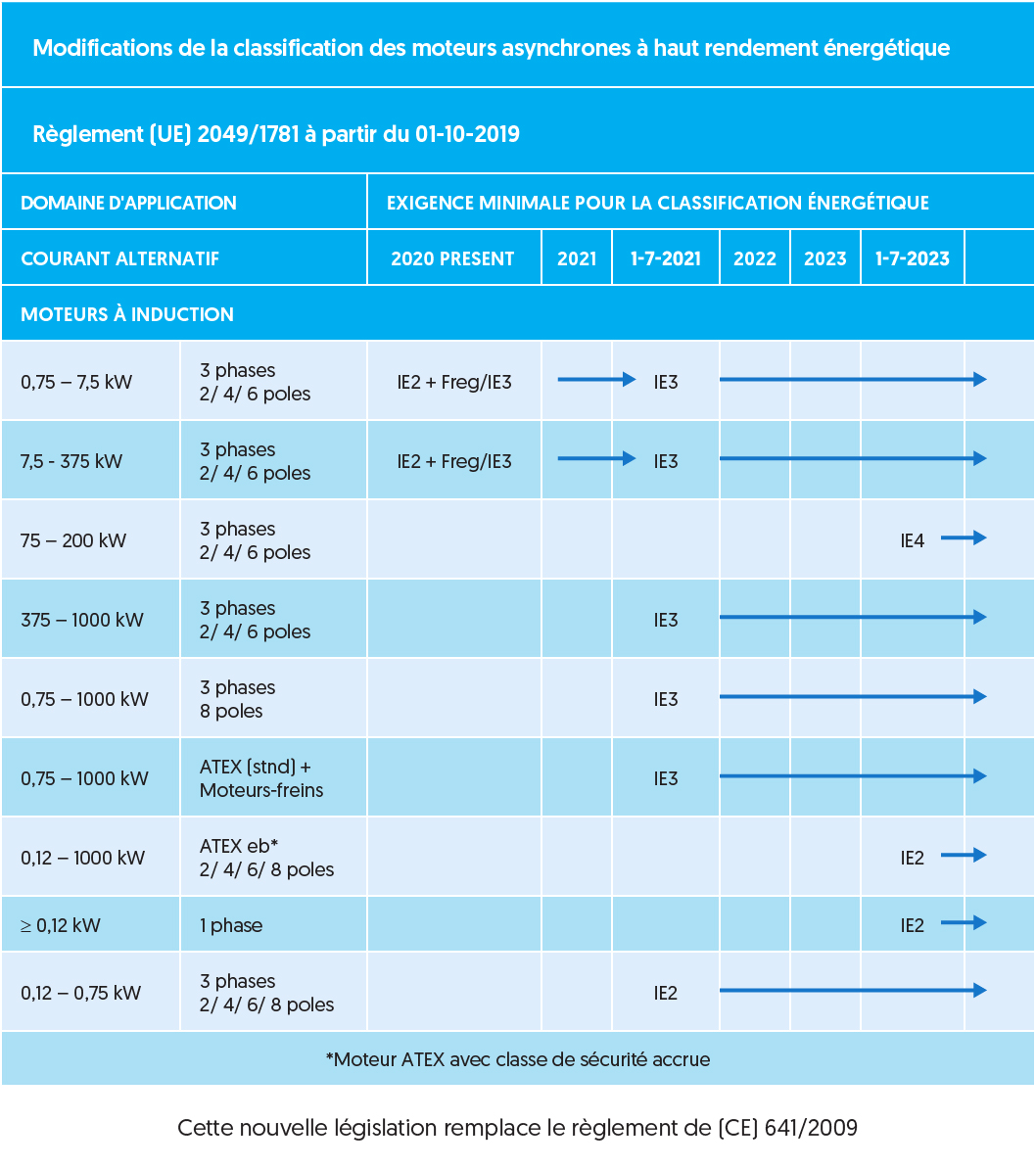
Figure 3 – Un aperçu des normes IE
Augmenter l'efficacité en Phase 2
La deuxième étape du règlement entrera en vigueur en juillet 2023, date à laquelle il sera obligatoire pour :
- tous les moteurs 75kW - 200kW, 2-4-6 pôles, de répondre au rendement super-premium IE4.
- les moteurs monophasés et les moteurs de sécurité Ex eb de 0,12 à 1000 kW de répondre aux normes de rendement IE2.
Bien que la norme IE3 soit désormais l'exigence légale, vous devez considérer le retour sur investissement (ROI) des moteurs classés IE3 par rapport aux moteurs classés IE4. Les moteurs de classe IE4 nécessitent un investissement initial légèrement plus élevé, mais le système est plus rentable et s'amortit facilement grâce aux économies réalisées sur les coûts énergétiques. En fait, ils présentent un retour sur investissement similaire à ceux des moteurs classés IE3. Une fois que le moteur aura été rentabilisé, il continuera à générer d'importantes économies d'énergie d'année en année, dépassant de loin celles obtenues avec un moteur IE3.
En allant au-delà des réglementations en vigueur, vous économisez non seulement un maximum d'énergie, mais vous préparez également votre système à tout changement de législation.
La valeur du coût total de possession
Étant donné qu'un pourcentage aussi élevé – 97 % – du TCO est entièrement imputable au coût de l'énergie électrique, il est clair que c'est là que vous pouvez réaliser le plus de gains. Il est essentiel de prendre en compte le TCO plutôt que l'investissement initial pour faire des économies.
Par exemple, le coût d'un moteur typique IE4 55 kW 4 pôles est de 3 264 €, mais le coût énergétique pour le faire tourner 24/24h et 7/7j est de 50 206,90 € (en supposant un coût énergétique de 0,1 €/kWh (voir figure 4).
Vous pouvez être tenté d'opter pour l'équipement dont le coût d'investissement est le plus bas, car vous aurez à première vue l’impression de faire une « meilleure affaire ». Toutefois, ces économies immédiates peuvent s'avérer préjudiciables aux bénéfices. Envisager des produits plus efficaces sur le plan énergétique signifie que les coûts du cycle de vie sont réduits, ce qui améliore le flux de trésorerie à plus long terme.
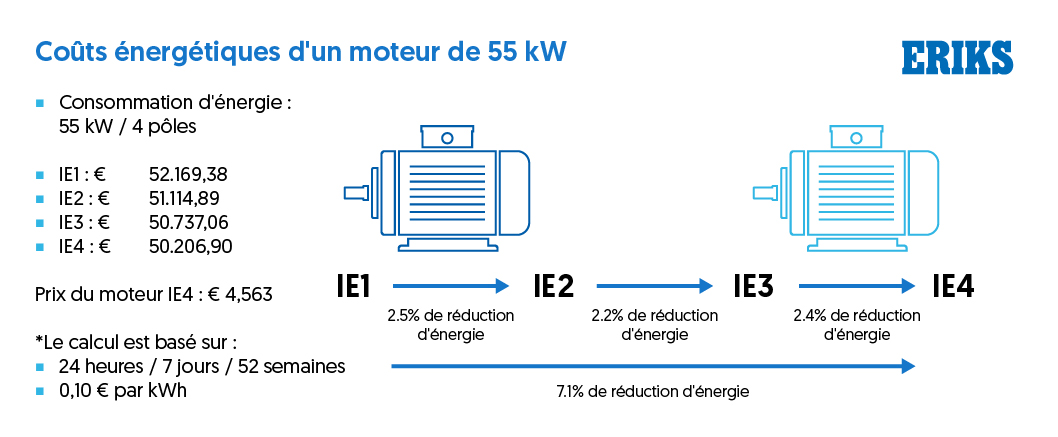
Figure 4 – les coûts d'exploitation des moteurs
Réparer ou remplacer
Lorsqu'un moteur tombe en panne, la réparation est souvent envisagée en premier lieu. Cette solution est souvent considérée comme une réparation rapide et peut, à première vue, coûter beaucoup moins cher qu'un nouveau moteur (en fonction de la réparation nécessaire).
Il peut toutefois s'agir d'une fausse économie, car un moteur âgé de 20 ans qui nécessite un entretien et des réparations réguliers vous coûtera plus cher à long terme. Remplacer un moteur plus ancien par un moteur plus moderne, élaboré dans une optique d'efficacité énergétique, vous rapportera des dividendes à long terme. Si votre moteur tombe en panne, vous devrez quand même le réparer ou en acheter un nouveau. L'investissement minimal que vous devrez faire est le coût de la réparation. Si vous décidez d'acheter un nouveau moteur, vous pouvez soustraire le coût de réparation du prix du nouveau moteur, ce qui réduit le montant total de l'investissement que vous devez récupérer, et améliore le retour sur investissement.
Par exemple, dans l'industrie alimentaire, le remplacement d'un vieux moteur de ventilateur par un moteur plus récent et plus efficace, a été rentabilisé en 10 mois seulement et s'est avéré plus rentable. Le moteur existant avait une puissance de 110 kW et un rendement de 91,6 %, et sa réparation allait coûter 3 950 €. Le nouveau moteur WEG 90kW IE3 avait un rendement de 95,6 % et un coût d'investissement de 6 745 €. Comme le montre la figure 6, les économies réalisées s'élèvent à 65 840 € sur la durée de vie du moteur et les émissions de CO2 à 196 tonnes.
Facteurs supplémentaires de réduction des coûts
Choisir le bon moteur est essentiel pour améliorer la fiabilité et l'efficacité énergétique, mais il existe également d'autres moyens de réduire la consommation d'énergie et les coûts de maintenance. La chaîne d'entraînement complète doit également être examinée pour avoir un impact maximal sur les économies de coûts. Travailler avec des partenaires de confiance qui connaissent parfaitement les solutions les plus écoénergétiques peut s'avérer payant lorsqu'il s'agit de comprendre où les économies peuvent être réalisées au mieux.
Par exemple, les VSD peuvent jouer un rôle majeur dans l'amélioration de l'efficacité tout en assurant une performance fiable et en réduisant les coûts de maintenance. Investir dans des moteurs électriques à haut rendement combinés à des VSD peut se traduire par des économies opérationnelles pouvant atteindre 20 %.
Les plus grosses économies peuvent être réalisées avec les applications à couple quadratique, telles que les pompes centrifuges ou les ventilateurs dont le débit est régulé par une vanne d'étranglement. En atténuant la vanne d'étranglement et en régulant la vitesse du moteur avec un onduleur, nous pouvons faire d'énormes économies. Beaucoup plus qu'en améliorant l'efficacité du moteur. ERIKS peut vous aider à calculer ces économies et le retour sur investissement associé, et à mettre en place le changement.
L'importance du dimensionnement
De plus, il est important de revoir le dimensionnement du moteur pour vérifier si le bon équipement est utilisé pour le travail en question. Par exemple, l'application dispose-t-elle d'un moteur de la bonne taille ou peut-on en utiliser un plus petit et plus efficace à la place ? Les analyseurs de puissance sont ici essentiels. Ils peuvent être utilisés pour mesurer la puissance réellement requise dans le système, afin que les moteurs puissent être dimensionnés en conséquence. Cela s'explique par le fait que l'efficacité d'un moteur électrique chute de façon exponentielle lorsque la charge descend en dessous de 70 % de la charge nominale. Par le passé, mais encore aujourd'hui, les fabricants ont tendance à surdimensionner le moteur car ils ne veulent prendre aucun risque.
Nous pouvons également nous pencher sur les autres éléments de la chaîne cinématique qui consomment de l'énergie et réduisent l'efficacité globale. Il arrive souvent que les chaînes et les courroies ne soient pas parfaitement dimensionnées, et parfois même pas du tout nécessaires. Il est possible d'analyser l'ensemble de la chaîne cinématique et de suggérer la configuration idéale en fonction des besoins du client.
Pour une application dans une entreprise laitière, un moteur à 4 phases de 132 kW de 30 ans était utilisé pour alimenter un compresseur de refroidissement. Toutefois, un analyseur de puissance a dévoilé que le moteur affichait seulement une consommation d'énergie de 88,9 kW. Le moteur tournait pendant 8000 heures par an avec une consommation d'énergie totale de 711 200 kWh. Le coût de l'électricité était de 0,06 ct/kWh, ce qui représente un coût énergétique total de 42 672 € par an.
Étant donné que l'analyseur de puissance a démontré que le moteur nécessitait seulement environ 90 kW, l'entreprise a optimisé son moteur en achetant un moteur de 90 kW noté IE3, plus efficace d'un point de vue énergétique. Après l'installation, une nouvelle mesure de la consommation d'énergie a été prise. Celle-ci a démontré que la consommation de puissance s'était encore plus réduite pour atteindre 82,5 kW. La consommation énergétique totale s'établissait à présent à 660 000 kWh pour un coût de 39 600 € par an.
Grâce à l'investissement dans un nouveau moteur IE3 plus petit, l'entreprise a été en mesure d'économiser un impressionnant montant de 3072 € par an. Le ROI (retour sur investissement) était de 1,92 an.
Conclusion
Améliorer l'efficacité énergétique des moteurs électriques peut avoir un effet important sur la consommation d'énergie globale et donc réduire les émissions de CO2 et économiser sur les coûts de fonctionnement.
Bien qu'il existe une législation visant à garantir que les fabricants utilisent des moteurs à haut rendement énergétique, de nombreuses entreprises industrielles s'efforcent également de respecter leurs propres indicateurs clés de durabilité afin de fonctionner aussi efficacement que possible. Un examen des moteurs utilisés tout au long des processus peut grandement vous aider à atteindre ces objectifs.
Il n'existe pas de solution universelle au moment de choisir le moteur et le système énergétiquement les plus efficaces, et une collaboration avec des spécialistes permet dès lors d'optimiser les bénéfices. Un accès à l'expertise adéquate, au savoir-faire en ingénierie et à un avis impartiel sont les principaux éléments nécessaires pour trouver une solution plus durable et plus rentable.
Soyons réalistes, qui ne voudrait pas économiser des milliers d'euros chaque année simplement en remplaçant un moteur ? Mais par où commencer ? Nos ingénieurs peuvent vous aider à trouver le moteur adéquat avec la norme appropriée et la puissance de sortie adaptée, en vue de faire le maximum d'économies en termes de coûts énergétiques.
Calculez vos économies en utilisant le Calculateur de TCO des moteurs et découvrez les solutions qui s'offrent à vous pour réduire le TCO de votre moteur.
Pour obtenir plus d'informations sur l'importance du TCO, n'hésitez pas à vous rendre sur cette page.
Abonnez-vous à notre newsletter:
Pour recevoir les actualités de l'industrie.